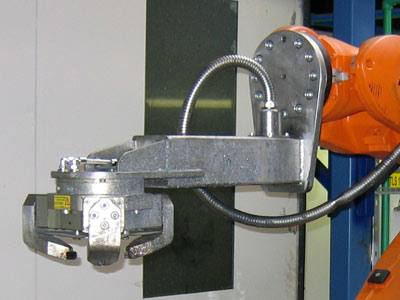 |
Foundry industry
Removal of compression aluminium castings from the injection press
The gripper is designed for removing aluminium castings at a temperature of 300°C from the compression press. With regard to the subsequent cooling of the manipulated product, the gripper is made entirely from stainless steel. Because of the high temperatures, the compressed air manifolds for controlling the jaws are integrated into the body of the gripper.
A standardized three-point gripping module made by Schunk was used in the structure. The gripper itself is installed on a six-axis robot ABB IRB 6640.
|
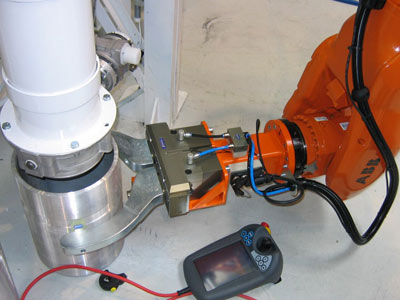 |
Automotive industry
Manipulation using 30 kg cups for loose polymer.
The gripper is designed and proportioned for manipulating Dural cups filled with loose polymer. The maximum cup weight is 30kg.
The gripper is equipped with sensors to register the presence of the cup and an ultrasound proximity sensor.
This construction also uses a parallel gripper made by Schunk. The gripper is manipulated by a six-axis robot ABB IRB 6600.
|
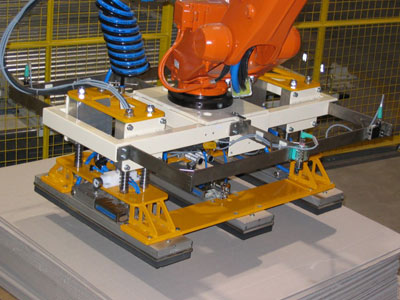 |
Pulp and paper industry
Manipulation with Euro pallets and cardboard inter layers.
The gripper is designed for manipulating wooden Euro pallets and cardboard layer pads. The basic element of the gripper is formed by three large-area suction cups, which are connected to the steel frame through spring loaded mounts.
The gripper is equipped with optical sensors for identifying the presence of a pallet or cardboard layer pad, and with ultrasound sensors, which inform the robot of its distance from the product when approaching it.
The gripper was constructed for the palletizing robot ABB IRB 660.
|
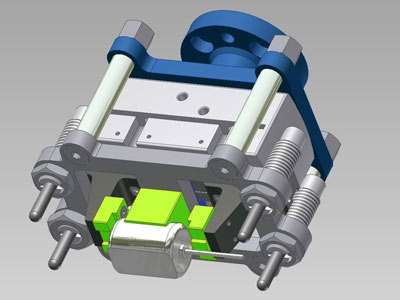 |
Automotive industry
Assembly of automobile components
The gripper is designed for assembly workstations where a robot installs additional components into a specific construction unit, in this case an electric motor. The gripper had to comply with strict requirements for precision and lack of weight. At the same time, a problem with the magnetic forces of the motors had to be solved because they “stuck” to each other when being removed from the pallet.
The construction uses a parallel gripper made by the company Festo; the gripper itself was designed for the ABB IRB 140 robot.
|
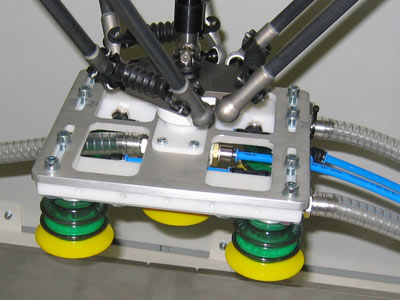 |
Food industry
Manipulation with bags full of food product
The gripper is a simple design used for manipulating plastic bags. The emphasis was given to weight and mechanical durability. The gripper is equipped with suction cups and bellows made by the company Piab.
The gripper was constructed for the ABB FlexPicker IRB 360 robot.
|